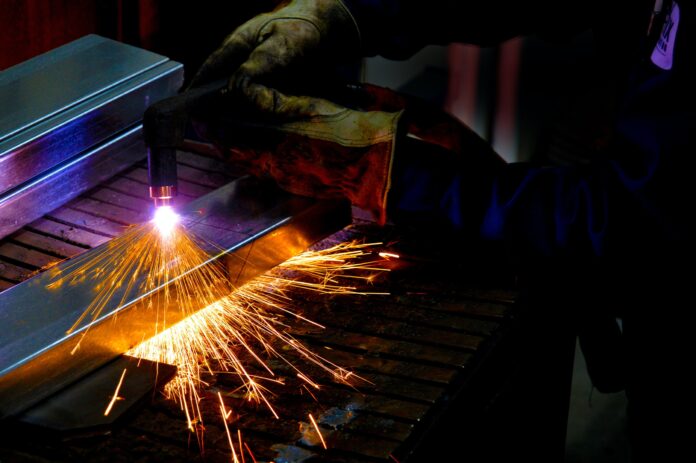
It is unlikely that you do not know what welding is, but if you do not know, it is the joining of two materials, usually two metals. The first forms of welding appeared a few thousand years ago, of course, the whole process was significantly different than today. From then until the 19th century when Sir Humphrey Davy invented the electric arc, improvements were so minor that they were barely noticeable. The arc brought a revolution, and then the Volta invented the voltaic cell and this allowed two different metals to connect.
That was the beginning of welding as we know it today. Until then, welding was practically forging, because the two metals were joined with the help of fire and hammers. Today, we live in an era when everything is advancing at the speed of light, and welding is no different. Constant improvements bring many new possibilities, and also make the whole process faster and safer. As welding is an indispensable part of every industry as well as construction, it is certain that new improvements will happen constantly. When you think and realize that man is now building buildings over 500 meters high, it is clear that various other improvements must happen in this field. And all this is closely connected with the progress of other technologies. So we will tell you the ways technology has changed welding in the last 20 Years, to understand how far we have come.
1. Different materials can be weld
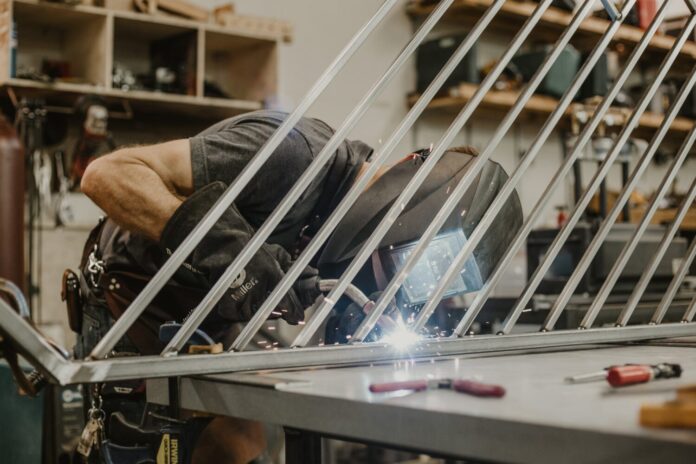
More and more different materials are used in all industries. The reasons for implementing these materials are varied and therefore, steel is no longer the material used in 90% of cases. These are various types of metals and alloys that have proven to be resistant, light and suitable for easy shaping, which is significantly more difficult when we talk about steel. While there are still many uses where steel is indispensable, many, like car factories, are increasingly using other materials. One of the main reasons is certainly the preservation of our environment which will be way too polluted within the next decade if we don’t take steps to preserve it.
However, new ways of welding these materials had to be devised, which were suddenly in use everywhere, and until a couple of decades ago, they did not exist, or we barely knew about them. This led to the advancement of laser welding, which we will talk more about later, and it is certainly one of the main ways in which technology has improved welding.
2. New types of welding
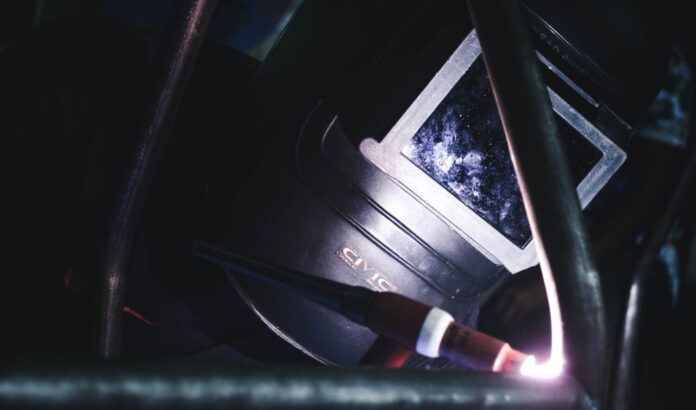
Arc welding, which we mentioned in the introduction as a revolutionary new method devised in the 19th century, is still a very popular welding method and is often used by both individuals and industries. But this traditional method has a lot of shortcomings and is not suitable for all materials and here we come to new types of technologies, more precisely welding.
Laser welding as the most important, but also friction stir welding as well as advanced arc welding.
Lasers are generally very advanced and have applications practically everywhere, from medicine to the military to welding. Lasers are used for these purposes when high speed welding is required, either because of the characteristics of the material or because it is necessary to complete a large amount of job quickly. Also, low thermal distortion is another great advantage of lasers. It should also be noted that weld seams are almost invisible when a laser is used.
Friction stir was invented in Cambridge and is based in a completely different way. The rotating tool presses the materials and then the materials are weld through the frictional heat and the fractional heat is obtained from the rotating shoulder of the machine. As with lasers, no filler materials are used. This method is used for alloys and a very high-quality weld is obtained. A filler is what is put between two things that you need to weld, in order to merge, if you didn’t know.
Advanced arc welding is an advanced traditional arc welding and gives a better quality weld that lasts longer.
3. Equipment upgrades
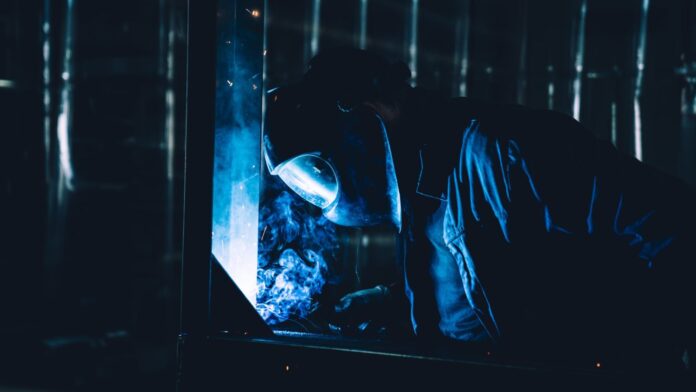
With the advancement of various technologies, we also get much better and safer welding equipment. We all know how important it is to have quality equipment during welding because different types of injuries can occur. Helmets are the part of the equipment that has advanced the most because the visors are multifunctional. In addition to protecting your face and especially your eyes and giving a clear overview of what you are doing, they also have some new features such as having an insight into the duration of welding and much more that significantly facilitates and improves your work. Also, helmets have buttons on them to easily change different options and so on. At welding.com.au, you can see the new types of helmets they look like, and gloves and other pieces of equipment are also safer than ever before.
4. Robotics
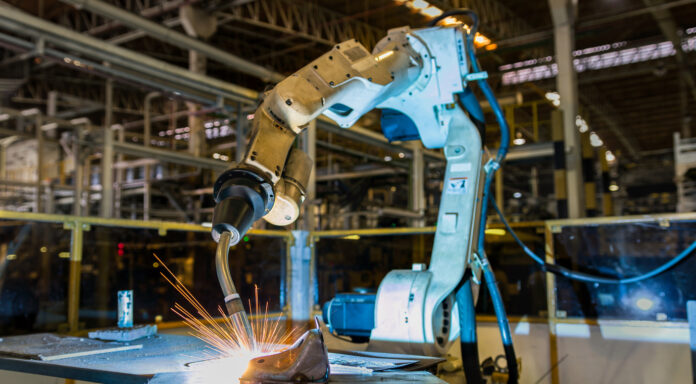
Robots are already an indispensable part of the automotive and many other industries and are increasingly used in welding. Robotics has been making major strides in recent years and it is only a matter of time before robots perform many other functions like surgeries.
Also, we expect that the time will soon come when robots will be able to perform the entire welding process. They are currently very efficient, but only with the control of a human operator. They are very precise, generate very little waste and can work any method, but it still takes a man to keep the quality at a high level.
Conclusion
Thanks to different types of technologies, we have reached a level where productivity is greatly increased. New welding machines, as well as the methods and equipment available to people, have led to the fact that today it is possible to do three or four times more work than before. Also, failures are very rare, which brings significant savings because you don’t have to do the same thing several times and waste time and resources.