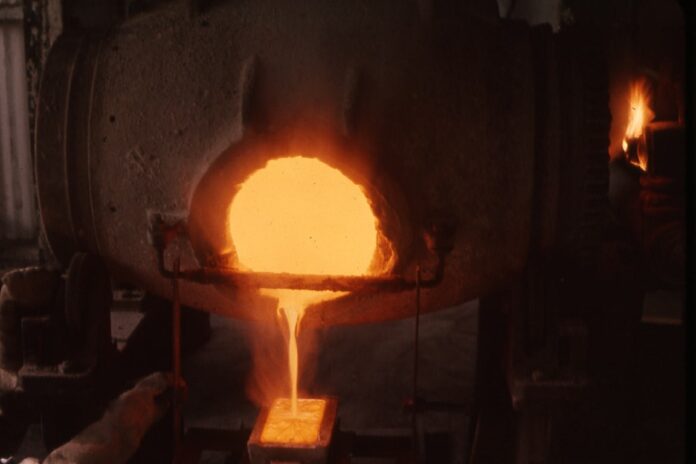
The metal industry is one of the most significant industries in developed countries. Today, the metal and machine industry are the most important industries for the economy – and they are closely related to the mining, foundry, and metal industry.
Metalworking involves using foundry furnaces, in which we use different types of furnaces as well as different techniques. Therefore, here are some of the types of foundry furnaces and their applications.
Foundry Procedure And Its Significance For The Metal Industry
The metal industry is of great importance in the economy of many countries. Yet many among us do not know numerous things related to this industry. As laypeople, we often tend to mix certain procedures in the metal industry because it all seems similar to us.
Many things in this industry differ – and foundry is one of such procedures. We must point out that the foundry procedure does not have to refer exclusively to metals – but also some other materials.
However, this process is best known for the foundry processing of steel, iron, and similar materials – because it is performed at high temperatures with the help of special furnaces for this purpose.
Casting Procedure
The casting of metals or other materials is performed in a foundry which is a plant that serves this purpose. The procedure itself involves melting the metal in special furnaces at high temperatures. Once metals begin to dissolve and soften, they will be cast into different shapes.
We can do this by placing the molten metals in special casting molds and allowing them to cool – after which the castings are removed from the molds to give the desired shape and size. Metals such as iron or aluminum are most commonly cast – but steel, bronze, brass, or zinc are equally common.
Each of these metals melts at different temperatures. For example, iron requires very high temperatures – and special foundry furnaces are used when we do this procedure. Foundry furnaces can be used in different techniques and achieve different temperatures. Therefore, we can classify them into several categories. Let’s see what this is about.
Types Of Furnaces Used In Foundry Processes
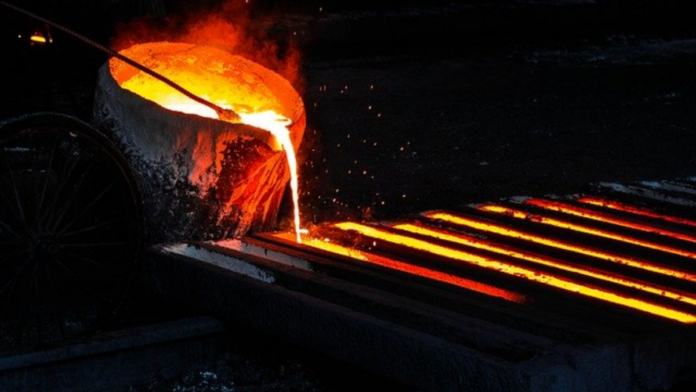
In the metal industry and foundry projects, everything revolves around the technology used in the casting process. This technology is not always used only for processing and dissolving metals – but is also used for the extraction of metals from the existing ores.
For something like that, we need large foundry plants with machines and foundry furnaces. We have several distinct kinds of foundry furnaces. Some of them are used only for dissolving metals, some for removing metals from ore or making alloys. However, the most typically used furnaces can be divided into four basic types.
1. Induction furnaces
Induction furnaces are the ones we will most often see in foundries. There are many reasons for this – and the primary reason is the non-complicated handling of these furnaces, which are usually used in the production of steel.
Experts claim that the average amount of steel that such a furnace can produce is more than 60 tons per charge. The system on which the induction furnace rests and operates is such that the steel is filled into an electromagnetic boiler wrapped in copper. In this way, vortices are created in the electromagnetic field – which causes the metal to melt.
According to dawangcasting.com, during this procedure, heat is generated by the excited metal molecules – and not by adding gasses or oxygen inside the furnace.
2. Dome furnaces
These are furnaces of characteristic shape, resembling a chimney. The energy needed for their functioning is obtained from coke coal, which is often mixed with various additives. The metal itself that we will melt is placed directly in the furnace. However, the fact is that such furnaces go down in history. Namely, in most foundries, people stopped using them – replacing them with induction furnaces which are far more efficient and economical.
3. Crucible furnaces
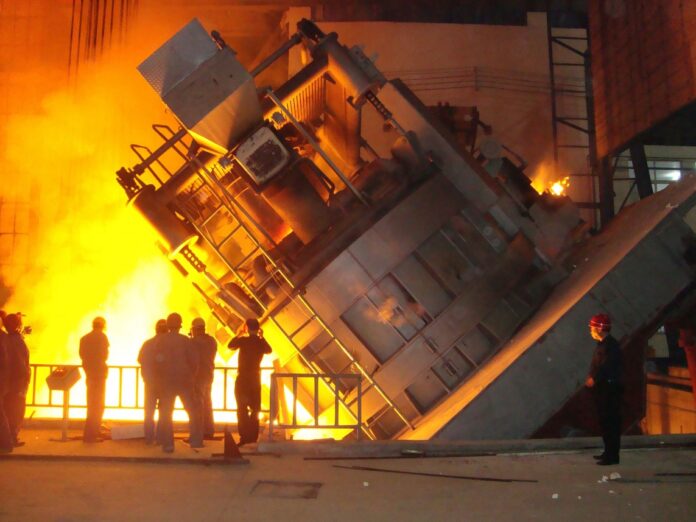
These are perhaps the simplest types of furnaces – that are often made from other refractory materials. One of the most commonly used materials is ceramics, which can withstand very high temperatures.
Working with such furnaces is simple – and involves placing a crucible filled with metal or some other material inside the heat source. The size of such furnaces can vary from very small to larger ones. However, we cannot melt large amounts of metal in them that would be necessary for industrial production – so such furnaces are most often used by jewelers or those who are engaged in a similar hobby.
4. Electric arc furnaces
As the name suggests, these furnaces are connected with the electric arc system. How do they work? For their functioning, they use electrodes – which have the role to drive an electric current through the metal that is inside the furnace itself. It is a graphite electrode that is positioned at the top of the furnace.
The electric arc system is stable in this case – and this makes even distribution of the heat inside the furnace possible. For this reason, such furnaces are very effective – and if you want to make the whole procedure even more efficient, oxygen can also be added.
Conclusion
Although smelting metals, extracting them from ores, and making alloys have been skills known to man since ancient times – many of us still do not know enough about casting processes or foundry projects. Therefore, we hope that we have brought this topic at least a little closer to you and clarified it.
These procedures are not only done for the production of steel or other metals – but have also found their application in other industries. Without furnace casting, we probably wouldn’t be able to do many things that modern industry, and above all people, take for granted today. In addition to the furnaces we have listed, there are others – such as those that add oxygen to the entire process or some other gasses that help burn and achieve high temperatures.
Nevertheless, we can say that these four types of furnaces are the most typical and most commonly used in practice.